
The design and manufacturing of pressure vessels require attention to various structural elements, with the connection between the spherical head and the cylinder being especially crucial. Spherical heads offer significant advantages in pressure containment, as they are more efficient than other head types. This article discusses the advantages of spherical heads, challenges with the connection structure, and potential solutions.
Advantages of Spherical Heads in Design
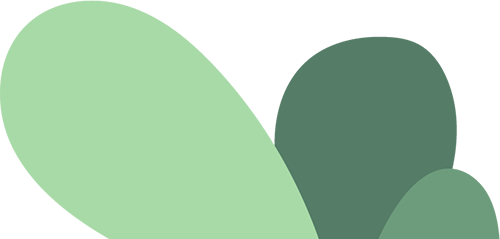
Advantages of Spherical Heads in Design
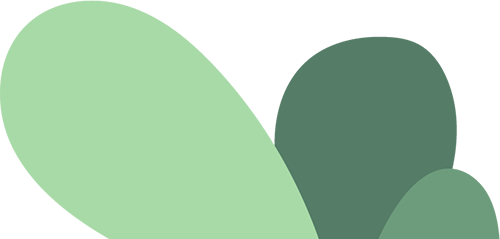
Spherical heads are ideal for bearing internal pressure due to their shape, which enables them to withstand pressure more effectively than other head types. For vessels of the same diameter and pressure requirements, spherical heads require thinner walls, resulting in material savings. This makes spherical heads particularly suited for high-pressure environments. However, the connection between the spherical head and cylinder is a critical factor that requires careful consideration to ensure the vessel's safety and efficiency.
Challenges with the Cylinder and Head Connection
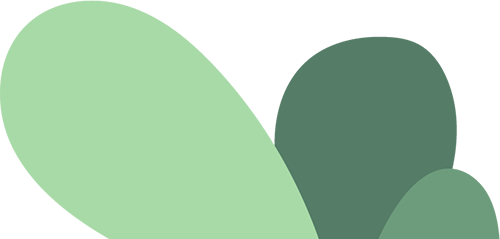
Challenges with the Cylinder and Head Connection
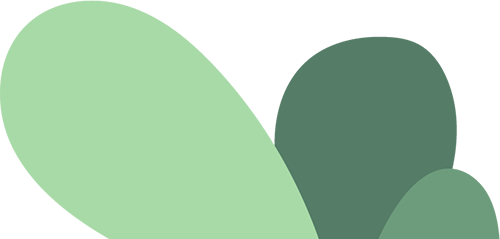
The primary challenge in designing pressure vessels with spherical heads is the significant difference in wall thickness between the cylinder and the spherical head. The cylinder typically has a much thicker wall, which makes it difficult to achieve a direct connection. China’s GB/T150 standard defines the weld between the cylinder and spherical head as a Class A welded joint, underlining its importance in ensuring the vessel’s structural integrity.
Cylinder vs. Spherical Head Wall Thickness
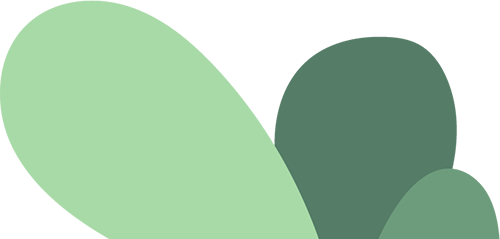
Cylinder vs. Spherical Head Wall Thickness
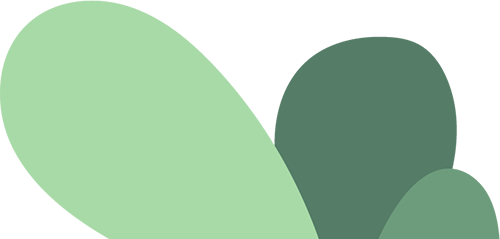
The required wall thickness for spherical heads is typically about half of that needed for the cylinder, even after accounting for the thickening during processing. This discrepancy in thickness makes direct connection difficult. If the cylinder is chamfered to match the spherical head, the resulting section may not meet the design specifications, compromising the vessel's safety. Moreover, increasing the cylinder’s wall thickness to compensate for the chamfered area would raise manufacturing costs significantly.
Solving Connection Challenges
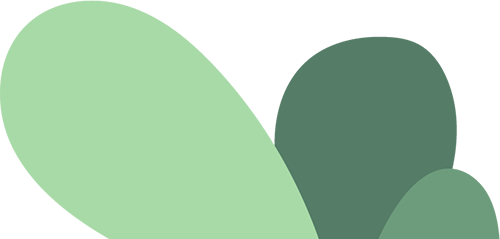
Solving Connection Challenges
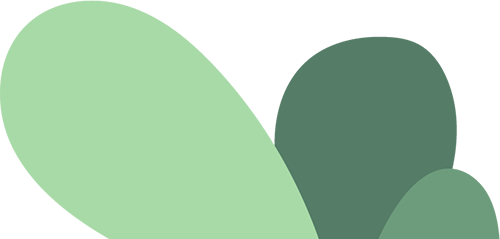
One solution is to chamfer the cylinder, gradually reducing its wall thickness to match the spherical head. However, this process must be done carefully to avoid weakening the cylinder’s structure. Another method involves applying cladding to thicken the cylinder’s end, which matches the spherical head’s thickness. While this solution meets design requirements, cladding materials are expensive and add to the manufacturing cost.
A more cost-effective approach is to thicken the spherical shell itself. By extending the cylinder and trimming the edges of the extended section, a smoother transition from the cylinder to the spherical head can be achieved. This ensures the continuity of the structure while meeting the necessary wall thickness. After chamfering, the wall thickness for the spherical shell will comply with safety standards.
Chamfering Pressure Vessel Connections
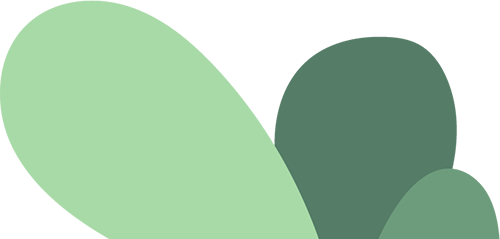
Chamfering Pressure Vessel Connections
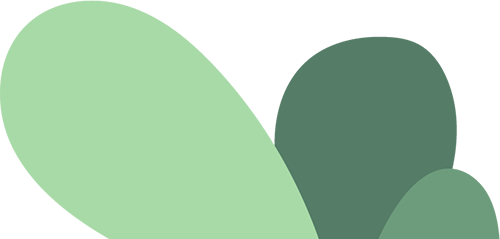
To ensure a quality chamfering process, it’s essential that the surface of the vessel is clean and free from contaminants such as oil or rust. The chamfering should be done using appropriate tools to ensure uniformity, and the edge should transition smoothly without sharp or jagged parts. Safety precautions, including the use of protective gear, should be followed during the process to prevent injury. After chamfering, a final inspection ensures that the dimensions meet design specifications.